In the world of metal fabrication and manufacturing, welding thin metal sheets presents a unique set of challenges. Excessive heat can warp or burn through the material, while inconsistent welds can compromise structural integrity and aesthetics. That’s where Argon arc welding, commonly referred to as TIG (Tungsten Inert Gas) welding, becomes an ideal solution. The argon arc welding machine is particularly well-suited for thin plate welding due to its precision, control, and clean finish.
Let’s explore why this welding technique outperforms other methods when dealing with thin materials.
1. Precise Heat Control
One of the most critical aspects of welding thin plates is managing heat input. If the temperature is too high or not well-controlled, the material can easily become deformed, warped, or even melted through.
The Argon arc welding machine, especially in TIG mode, offers excellent heat control through:
Adjustable amperage: Welders can fine-tune current levels to suit the material thickness.
Foot pedal or fingertip control: Allows real-time adjustments during welding.
Low start current: Reduces the risk of burn-through when initiating the arc.
This precision is essential for welding materials like stainless steel, aluminum, or carbon steel plates under 3 mm thick.
2. Stable and Focused Arc
The arc generated by an Argon arc welding machine is extremely stable and narrow, which concentrates the heat precisely where it’s needed. This focused arc:
Minimizes the heat-affected zone (HAZ).
Reduces the chances of distorting nearby areas.
Provides a clean, well-defined weld line.
Unlike MIG or stick welding, which tend to create a wider arc and more spatter, argon arc welding allows fine control of the weld bead — essential for thin metals.
3. Non-Consumable Tungsten Electrode
Argon arc welding uses a non-consumable tungsten electrode, meaning the electrode does not melt during welding. This characteristic:
Prevents contamination of the weld.
Keeps the heat input focused solely on the base metal and filler rod (if used).
Allows autogenous welding (welding without filler) for very thin materials, reducing additional heat and material usage.
This is particularly useful when welding thin stainless steel sheets or pipes, where adding filler could cause excess build-up or distortion.
4. Inert Gas Shielding with Argon
Argon gas plays a vital role in this welding process. As a chemically inert gas, it provides an effective shielding environment around the weld pool, protecting it from atmospheric contaminants such as oxygen, nitrogen, and hydrogen.
Benefits include:
Oxidation-free welds, even on highly reactive metals like aluminum and titanium.
Improved arc stability and cleaner weld appearance.
Reduced need for post-weld cleaning, which is especially valuable in visible or sanitary applications.
This clean and protected environment ensures better weld quality, which is critical when dealing with thin, high-precision components.
5. Minimal Spatter and Post-Processing
Welding thin plates typically demands aesthetic quality and surface integrity. Argon arc welding is renowned for producing:
Virtually spatter-free welds.
Smooth weld beads with minimal defects.
Very little slag or residue.
This is ideal for applications like decorative stainless steel panels, kitchen equipment, and aerospace components — all of which use thin plates and require high surface quality.
6. Support for Delicate Materials
Thin plates are often made of sensitive or high-value materials like aluminum, stainless steel, or even titanium. These metals are easily damaged by:
Overheating
Contamination
Rough handling
Argon arc welding is gentle and adaptable to these materials. It supports AC (alternating current) for aluminum welding and DC (direct current) for most other metals. Moreover, the process is manual and slow by design, giving welders time to make careful, detailed welds.
7. Applications in Thin Plate Welding
Thanks to these advantages, argon arc welding machines are widely used in:
Aerospace: Aircraft skin and engine components.
Food-grade equipment: Stainless steel surfaces requiring smooth, sanitary welds.
Automotive repair: Exhaust systems and body panels.
Medical devices: Stainless steel surgical instruments or enclosures.
Art and design: Metal sculptures and high-end fixtures.
In all these fields, thin plates must be welded with absolute accuracy and minimal deformation, making argon arc welding the go-to method.
8. Limitations to Be Aware Of
While ideal for thin plates, argon arc welding is not without drawbacks:
Slower welding speed compared to MIG welding.
Requires higher operator skill to maintain quality.
Equipment may be more expensive upfront.
However, for precision work and delicate materials, the benefits far outweigh these limitations.
Argon arc welding machines are more suitable for thin plate welding because they offer unmatched control, precision, and cleanliness. With their stable arc, low heat input, minimal spatter, and inert gas shielding, these machines help avoid common problems like burn-through, warping, and surface contamination.
Whether you’re working with stainless steel kitchenware, aluminum panels, or titanium medical tools, the argon arc welding process delivers superior results — especially when quality and precision matter most. For professionals and serious hobbyists alike, this technology remains the best choice for welding thin materials safely and effectively.
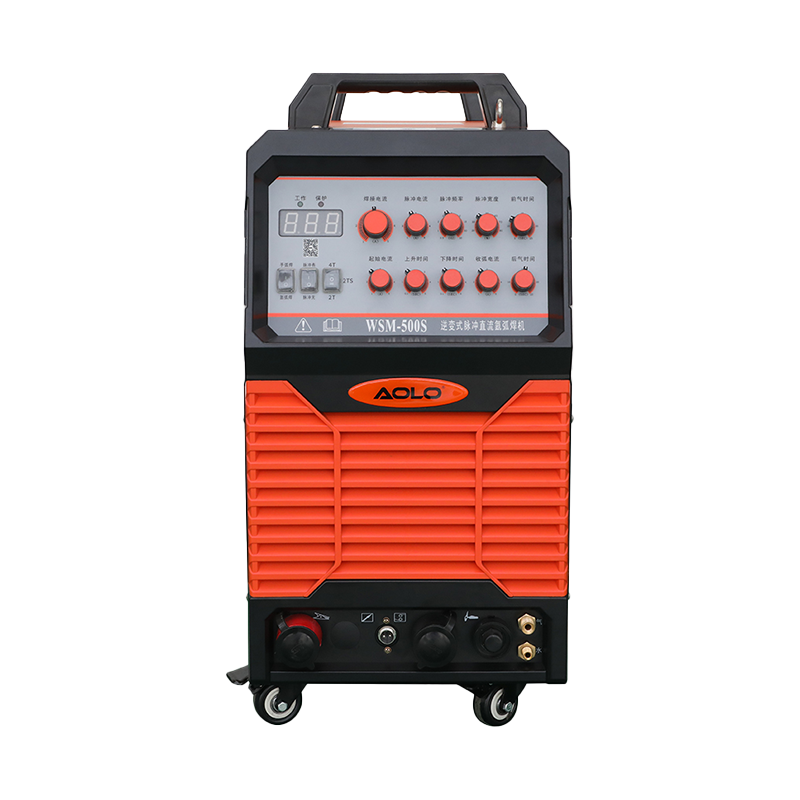
Contact Us