As an efficient and reliable metal connection equipment, Stud Welding Machine is widely used in industrial fields such as shipbuilding, bridge construction, automobile assembly, and steel structure engineering. However, in the actual operation process, it often faces a variety of complex working conditions such as high temperature, humidity, dust, and vibration, which puts higher requirements on welding quality and safety. So, how does the stud welding machine ensure the stability of the welding process and the safety of the connection quality under these adverse environments?
The stud welding machine adopts advanced power supply control technology, which is the core technical basis for maintaining welding stability in complex environments. Modern stud welding equipment is mostly equipped with an inverter power supply system, which can achieve precise control of current, voltage, and welding time. Even under conditions of large fluctuations in the power grid or unstable on-site power supply, the consistent output of welding energy can be guaranteed, thereby avoiding problems such as cold welding and burn-through caused by unstable energy, and improving the strength and reliability of the welded joint.
The welding process itself has a highly automated characteristic, which effectively reduces the safety hazards caused by human operation errors. For example, in the process of arc stud welding and capacitor discharge stud welding, the entire welding action is automatically completed by the equipment, including arc striking, melting, pressurization and cooling, which are all precisely controlled by the program. This high-precision automated process allows the consistency and repeatability of welding quality to be maintained even in high-altitude operations, confined spaces or construction sites with large vibrations.
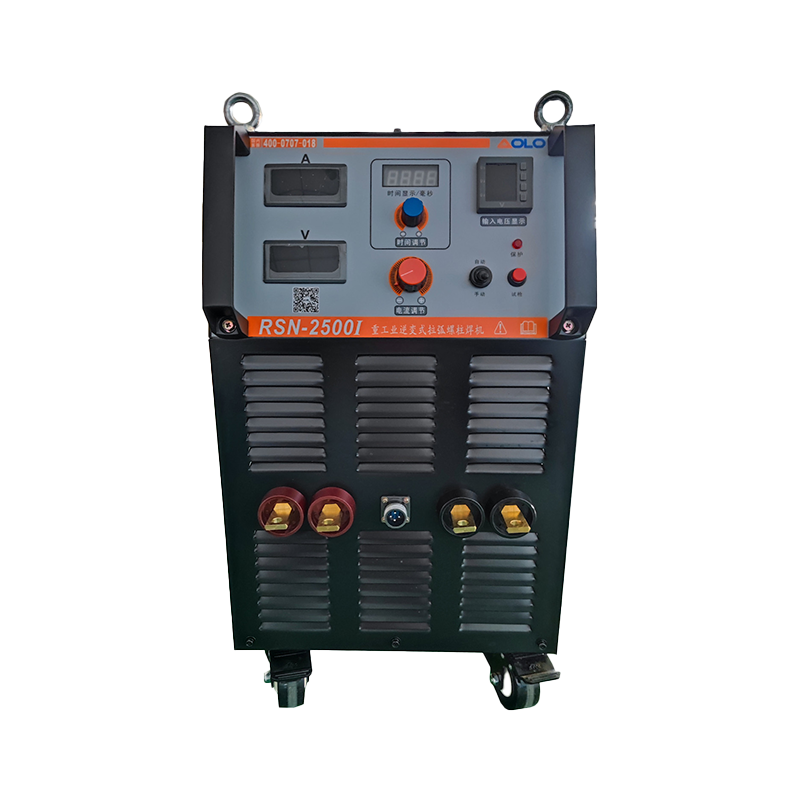
The dedicated welding fixtures and shielding gas systems used by stud welding machines also play a key role in welding safety in harsh environments. In windy, dusty or rainy outdoor construction environments, the welding area is easily disturbed by the outside world, resulting in weld oxidation or slag inclusions. For this reason, many high-end stud welding equipment is equipped with gas shielding devices (such as argon or mixed gas), which can form a stable protective layer during welding to prevent the weld from being destroyed by oxygen in the air, thereby improving the density and corrosion resistance of the weld.
The real-time monitoring of welding parameters and fault warning functions further improve the safety of the equipment under complex working conditions. At present, most intelligent stud welding machines on the market are integrated with digital control systems, which can monitor key parameters such as welding current, voltage, time, etc. in real time, and feedback data through display screens or remote interfaces. Once an abnormality is found, the system will immediately sound an alarm or even automatically stop running to prevent the occurrence of unqualified welding and eliminate safety hazards from the source.
Strong material adaptability is also one of its important advantages in dealing with complex environments. Stud welding technology is not only suitable for conventional metal materials such as carbon steel and stainless steel, but also for welding special materials such as aluminum alloys and galvanized steel plates. This enables it to be flexibly applied in different climatic conditions, chemical corrosion environments, and high temperature and high pressure occasions to meet the diverse requirements of various projects for welding joint performance.
With its precise power supply control, high degree of automation, perfect gas protection system, strong intelligent monitoring capability and good material adaptability, the stud welding machine can still ensure the safety and stability of welding quality under complex working conditions. With the development of intelligent manufacturing and Internet of Things technology, future stud welding equipment will be more intelligent and integrated, providing more efficient and safer welding solutions for various difficult construction scenarios.
Contact Us