With the increasing demand for intelligent manufacturing and efficient processing, 3 in 1 Laser Cleaning Welding Cutting Machines are becoming important equipment in modern industrial production. This type of equipment integrates laser cleaning, welding and cutting functions, which not only saves space and equipment investment costs, but also significantly improves processing efficiency and process adaptability. So, how does this type of multifunctional laser equipment achieve the dual improvement of efficiency and flexibility?
In terms of improving production efficiency, the biggest advantage of 3 in 1 laser equipment is "one machine for multiple uses", which avoids the downtime caused by frequent equipment replacement or process switching in traditional processing. For example, in the process of automobile manufacturing or ship repair, the same workpiece may need to be first surface rust removal and cleaning, then precision welding, and finally cutting and trimming. The traditional method requires the use of three devices and multiple operators separately, while the 3 in 1 laser equipment can complete all processes on the same workstation, greatly shortening the operation cycle and improving the degree of automation.
The application of intelligent control system makes the equipment have higher operational flexibility. Modern three-in-one laser equipment is usually equipped with CNC numerical control system and automatic identification module, which can quickly switch working modes according to different materials, thicknesses and process requirements. For example, through the preset parameter library, users only need to select the material type to automatically adjust key parameters such as power, frequency, and focal length to ensure that each process achieves the best effect without manual repeated debugging, which reduces the operation threshold and reduces human errors.
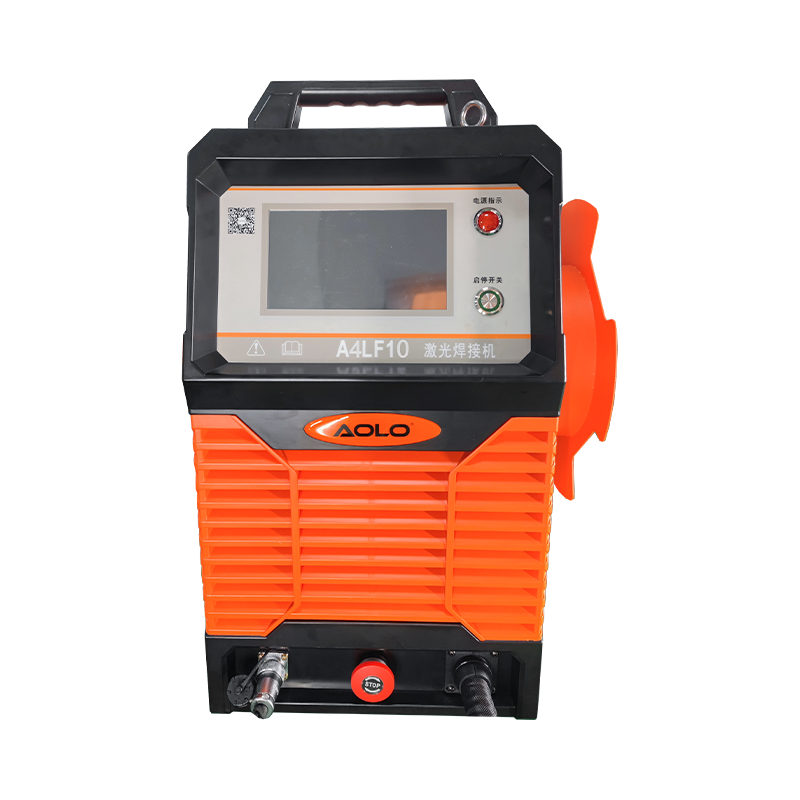
Multifunctional integrated design helps optimize workshop layout and resource utilization. Traditional processing lines often require multiple independent devices to occupy a large amount of space and are equipped with complex logistics and transportation systems. The 3 in 1 laser equipment integrates functional modules to reduce the footprint, which is especially suitable for small and medium-sized enterprises with limited space or on-site maintenance scenarios. In addition, the integrated structure also helps to unify maintenance standards and reduce equipment failure rates and maintenance costs.
In addition, environmental protection and energy-saving characteristics are also key factors in improving the sustainability of industrial manufacturing. The laser cleaning process does not require chemical reagents, reducing wastewater discharge; laser welding has a small heat-affected zone, low energy consumption and high precision; laser cutting is contact-free, without tool wear, and has higher material utilization. The combination of these three functions enables enterprises to better cope with increasingly stringent environmental regulations while meeting high-quality processing needs.
Wide applicability enhances the industry adaptability of the equipment. 3 in 1 laser equipment can be applied to many fields such as metal, composite materials, coating removal, etc., covering aerospace, rail transportation, automobile manufacturing, mold repair, electronic packaging and other industries. Whether it is cutting and welding of stainless steel, aluminum, and copper, or efficient cleaning of oxide layers, paints, and oil stains, it can be competent, showing extremely high application expansion potential.
3 in 1 laser cleaning welding and cutting equipment effectively improves the efficiency and flexibility of industrial manufacturing through integrated design, intelligent control, efficient processing flow and green environmental protection concept. It not only represents the development direction of future laser processing equipment, but also provides more competitive technical solutions for manufacturing companies.
Contact Us