In modern manufacturing, welding technology is one of the core processes for connecting metal structures and ensuring engineering safety. Among the many welding methods, Submerged Arc Welding Machine is widely used in heavy industries such as shipbuilding, pressure vessels, steel structure bridges, and pipeline engineering due to its high efficiency, high quality, and high degree of automation.
The basic working process of Submerged Arc Welding Machine is as follows:
Wire feeding system: The wire is stably delivered to the welding area through the wire feeding mechanism;
Power supply system: Provides stable current to maintain arc burning;
Flux supply and recovery device: Lays flux before welding and recovers unmelted flux after welding for reuse;
Walking or positioning system: Controls the moving trajectory of the welding gun according to process requirements, which can be manually operated or fully automatically controlled.
The whole process can be operated in automatic or semi-automatic mode, suitable for long straight seam and circumferential seam welding in flat welding position, especially suitable for large-scale welding tasks of thick plate materials.
Submerged arc welding can use a larger welding current, and the wire feeding speed is faster, so the deposition efficiency is high, which is suitable for one-time penetration welding of thick workpieces.
Excellent welding quality
The welding process is carried out under the protection of flux, the molten pool is not easily polluted by air, the weld is beautiful, there are few internal defects, and it has good mechanical properties and crack resistance.
Low production cost
Due to the fast welding speed, high utilization rate of filler metal, and recyclable flux, the overall welding cost is relatively low.
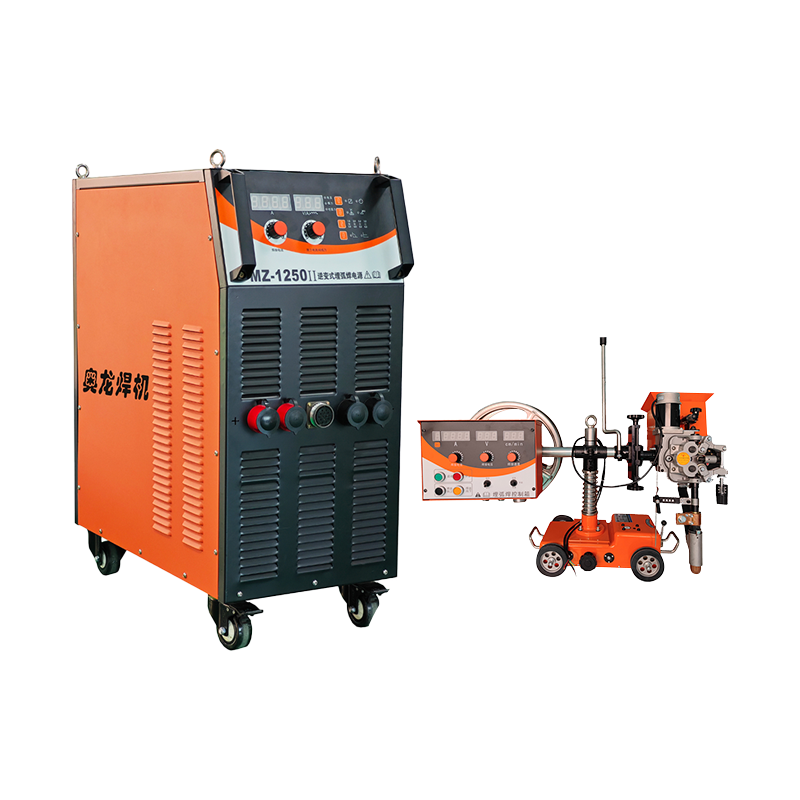
Good environmental performance
There is almost no visible arc light during welding, very little spatter, and less harmful gas is generated, which is conducive to improving the working environment of workers and conforms to the concept of green manufacturing.
Easy to automate
Submerged arc welding machine can be used in conjunction with welding manipulators, positioners, robots, etc. to achieve highly automated production and improve welding consistency and production efficiency.
Shipbuilding: used for butt joint and fillet welding of hull structural steel plates;
Heavy machinery and equipment: welding of large components such as crane beams and excavator arms;
Oil and gas pipelines: suitable for factory prefabrication and on-site welding of long-distance transmission pipelines;
Steel structure buildings: welding of main beams of large steel structures such as bridges, gymnasiums, and factory buildings;
Boilers and pressure vessels: key parts with extremely high requirements for welding sealing and strength.
With the development of intelligent manufacturing and digital technology, modern submerged arc welding machines are evolving towards intelligence, modularization, and energy saving. For example, integrated PLC control systems, remote monitoring functions, and automatic adjustment of welding parameters make the welding process more accurate and controllable. In addition, in order to adapt to more complex product structures, flexible welding systems and multi-axis linkage equipment are also emerging.
However, submerged arc welding also has certain limitations. For example, it is mainly suitable for flat welding positions and is difficult to perform full-position welding; it has high requirements for welding groove processing accuracy; and the equipment investment is relatively large, which is suitable for mass production and professional workshops.
Submerged Arc Welding Machine has become an important pillar equipment for modern industrial welding with its high efficiency, high quality and environmentally friendly welding characteristics. It plays an irreplaceable role in both infrastructure construction and high-end equipment manufacturing. In the future, with the continuous development of new materials and new processes, submerged arc welding technology will continue to be optimized to provide more powerful and intelligent welding solutions for the global manufacturing industry.
Contact Us